You are here: - Home
- Technical Support
- Some Issues Require To Be Paid Highly Attention During 7 Segment LED Display Soldering Process
Some Issues Require To Be Paid Highly Attention During 7 Segment LED Display Soldering Process
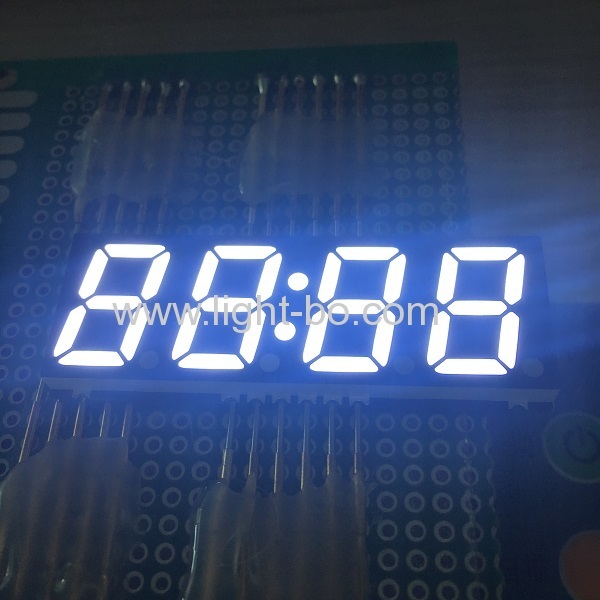
Many customers don't understand the characteristics of 7 Segment LED Display, so the employees' carelessness in the soldering process will lead to the bad phenomenon of LED display products. Therefore, during the soldering process of LED display, the following requirements must be strictly observed:
-Workers must wear antistatic gloves and wrist during production and operation, and the electric soldering iron must be grounded.
- The welding temperature of LED digital tube is 260 ℃, 3 seconds. If the temperature is too high or the time is too long, the LED chip will be burned. In order to protect the LED display better, the distance between the LED display gel and the PC board should be more than 2mm, so that the welding heat can be dissipated in the pin.
-The normal working current of LED display is 5mA-15mA, and small fluctuation of voltage (such as 0.1V) will cause large fluctuation of current (10% - 15%). Therefore, in the circuit design, different current limiting resistors should be matched according to the LED voltage drop to ensure that the LED display is in the best working condition. If the current is too large, the LED display service life will be shortened . If the current is too small, it will not reach the required light intensity.
SolderingTemperature of 7 Segment LED Display
There are two kinds of soldering, one is soldering iron, the other is wave soldering. Different soldering methods have different requirements.
Iron Soldering: the tip temperature of soldering iron (maximum 30W) shall not exceed 300 ℃; the welding time shall not exceed 3 seconds; the welding position shall be at least 2mm away from the colloid.
Wave soldering: the maximum temperature of immersion soldering is 260 ℃; the immersion soldering time shall not exceed 5 seconds; the immersion soldering position shall be at least 2mm away from the colloid. LED display soldering curve pin forming method:
-It must be 2mm away from the colloid to bend the bracket.
-Support forming must be completed by clamps or professionals.
-The support shall be formed to ensure that the pin and spacing are consistent with those on the circuit board.
-Support forming must be completed before welding.
Above are some problems in the soldering process of 7 Segment LED Display. Hope you can understand its relevant knowledge and make better use of them..